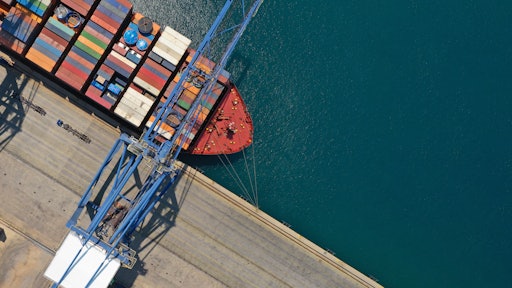
Port closures and congestion will remain until a resolution presents itself to restore supply chain predictability. At the time of publication there are still several unresolved concerns that hinder a return to some level of predictability for 2022, and possibly into 2023. This piece utilizes Aberdeen insights to shine a light on the current disruptions, as well as provide actions to take if things continue in this way.
What’s causing these disruptions?
The past two years have brought about a tremendous amount of supply chain disruptions sparked by a global pandemic. Initially, the pandemic caused numerous economic shutdowns, particularly retail businesses, creating significant shifts in buyer behavior for virtually all products.
As businesses were returning to new levels of equilibrium, the pandemic still had an impact on port closures. These closures created further shipment delays, resulting in product shortages for any products routed through those specific ports. In fact, Aberdeen data from its Q3 2021 Transportation Survey indicated that 29% of supply chain and transportation leaders reported that their supplier/carrier capacity did not meet the demand.
Further disruptions were also reported related to port congestion and customs delays, with 24% of supply chain and transportation leaders indicating that unexpected customs delays were a major factor. This was reported just as the U.S. West Coast ports container ship backlog started to climb, and there has not been any meaningful improvement since. The reasons given range from truck shortages to haul away the containers, driver shortages, overall port capacity to handle the volume, scheduling conflicts that created inefficiencies, and other variations on these possible causes.
Another significant factor contributing to the disruptions is that 29% of supply chain and transportation leaders have pinned fuel price volatility (due to oil price increases) as an extremely disruptive element controlling the costs for all goods. All companies found themselves shopping for the “best price” which added to some of the shipment delays. The net results for supply chain leaders are increased supply chain costs from fuel price increases and continued shortages due to port closures and congestion, as well as insufficient carrier/container/shipment capacity to support the demand.
Current events drive additional disruptions
In addition to congestion and delays that supply chain and transportation leaders are seeing at the ports, they also have protests and demonstrations driving further disruptions. At its third week, a trucker convoy set up in Ottawa peaked with an estimated 50,000 Canadian truckers or more surrounding the city in a peaceful demonstration in protest of current government mandates.
Further intelligence indicates that there is a carryover from Ottawa to the U.S., with reportedly an estimated 400,000 truckers or more in route to Washington DC at the time of publication.
There is also a worldwide carryover from Ottawa to international truckers in their individual countries, that are joining in effort to protest existing government mandates.
Resulting supply chain implications
There was already an existing shortage of capacity prior to any of the trucker convoys in Ottawa and US projections. Reducing or removing the number of serviceable trucks and drivers available by an estimated 50,000 in Ottawa plus another estimated 400,000+ from the US, from the existing framework to support the movement of goods across North America will have a compounding effect on already tight supplies and existing shortages for all products including food and medicines.
Shortages in stores will get progressively worse until issues are somehow resolved that would free up carrier capacity and get trucks back into service.
For those retailers, distributors, and brand manufacturers that have available product with some backup and control over their existing supply chain, might consider rationing the goods they have, based on their current outlook, in order to support as many customers as possible.
Business pressures for the remainder of 2022 (and into 2023)
Recent data from Aberdeen’s February 2022 Supply Survey provides a fresh perspective on the prognosis going forward regarding immediate business pressures and disruptions that are top-of-mind. It’s with no surprise that increased supply chain disruptions top the list.
Additionally, continued port delays on the west coast of the US will continue until some outside intervention occurs to reduce the backlog. No meaningful progress has been made in the last several months since backlog increased to over 100 ships.
Actions to take
If feasible at all, in order to maintain or increase supply chain buffers, manufacturers distributors and retailers might want to consider further warehousing space, and climate control storage to maintain larger buffers if they can get their hands on the products in short supply. Even if the price is higher, having any stock at all is the issue. Even renting space might be a wise short-term investment to weather the storm if they can find available product.
In the meantime, until issues are dealt with accordingly and corrective actions are taken, consumers should brace for longer shortages in the short term and focus on essential needs in areas or alternatives where they are currently seeing a shortage.