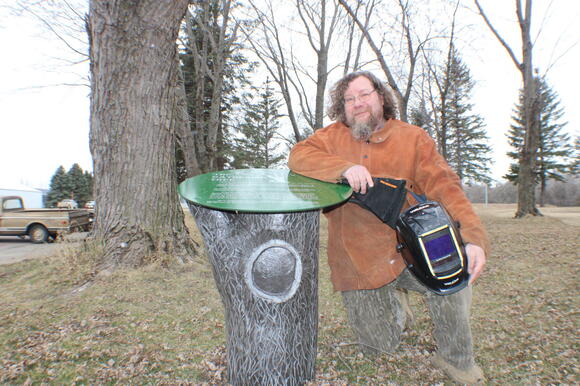
Since 2017, the Gathering Tree in Mothers Louise Park has been a shining testament to the power of community cooperation. The 85,000 bulbs, hung up by two dozen volunteers, light up the night sky each year during Le Sueur’s annual Christmas in the Valley celebration.
But now the Gathering Tree’s days are numbered. Two years ago, the city found the tree was harboring an emerald ash borer infestation. The wood boring pest has been responsible for the deaths of over 15 million ash trees across the US and Canada since 2002 and has been spreading throughout Southern Minnesota in recent years. While the Gathering Tree is receiving treatments to prolong its life, the pest can only be held off for so long before the tree perishes.
To commemorate the Gathering Tree’s legacy and teach the community about the threat of the emerald ash borer, local fabrication and restoration artist Johnny Favolise debuted a sculpted replica of the tree at last year’s Christmas in the Valley. The metallic structure is nearly identical to the tree, but instead of branches, the miniature is topped with a plaque detailing the history of the Gathering Tree and the harms posed by emerald ash borer.
Now, community members can see how this replica got made, from its beginning as a 3D design model to its final stage as a completed sculpture, in a 17-minute video documentary recently released on Favolise’s YouTube channel. The President of aDDDvantage Creations Inc. and iBother Studio carefully documented the month’s worth of work to give others an insight into the metal fabrication and design process and educate students interested in metalwork as a career path.
“The amount of time that it takes, you can’t slap something like this together. There’s a lot of love, effort, bleeding. I’ve got burns on my hands from welding,” said Favolise. “I think there’s a greater appreciation when they see the method.”
The sculpture is just one of the many unique projects that Favolise takes on at his Johnny Fab’s workshop at 549 Elmwood Avenue. With the assistance of 3D modeling, 3D printing and laser engraving technology, Favolise uses his fabrication skills to craft custom gifts and parts for vintage vehicles and antiques that can be difficult or downright impossible to replace.
Favolise is at his happiest when taking on a challenging project that an ordinary repair shop couldn’t handle. He has rows of stripped down vintage Harley Davidson motorcycles receiving custom repairs, while his own creations can be found around every corner from the windchimes by the entryway, to a laser-engraved welcome mat and a modified LED-lit welding mask.
The fabrication artist has even branched out into the paranormal. With the help of his father Peter, Favolise recently designed an electronic box, with “Yes” and “No” switches to help paranormal investigators ask ghosts yes-or-no questions. Favolise said the switches can only be activated by direct contact, making them more difficult to trigger than conventional paranormal detectors.
“The whole idea behind this is we wanted to put something that gets rid of all the other fluff that’s in there. You’re either having contact or you’re not,” said Favolise, who plans on taking the device out to market.
But Favolise’s most intensive undertaking at the moment are his efforts to restore a 1963 Cadillac Eureka hearse for paranormal investigator and Unscripted Paranormal host Adrian Lee. Sitting in a Wisconsin field for 38 years, its body was largely intact when it came to Favolise’s shop, but the interior was rotted out and the engine was frozen. After having recent success getting the engine fired up, Favolise aims to fully renovate and repair the hearse into a Ghostbusters Ectomobile complete with a laser-engraved logo.
Projects such as these have been Favolise’s bread and butter since the COVID-19 pandemic. The workshop space was originally meant to be a studio for the employees of his fitness facility design company, but when gyms across the country were shut down in response to the pandemic, Favolise’s customer base was almost completely wiped out. So Favolise turned around in 2021 and converted the space into his own personal workshop to pursue his passions.
“If I was going to reinvent myself, it was going to be what I liked doing,” said Favolise.
The fabricator’s process is on full display in the documentary, which takes viewers step-by-step through the construction of the Gathering Tree sculpture. Before even grabbing a piece of scrap metal or picking up a welding torch, Favolise first turned to his computer, where he mocked up a 3D model of the tree based on photographs. He then 3D-printed the model and presented the proof of concept to the Christmas in the Valley Committee.
With the committee’s approval. Favolise went to design measurements for an interior steel structure to help support the heavy, metal disc-shaped placard on top. Using recycled parts from a filing cabinet, which were cut, sanded, hammered and welded together, Favolise had his interior structure by the second week of November.
A rectangular stainless steel column with a single cylindrical branch, the interior structure was far from resembling a tree. But that would soon change when Favolise got to work on the most arduous part of the process, designing a bark-like casing. The steel materials were cut, hammered, planished, snipped, fitted, hammered again and tack welded into place to create a shape that resembled the curving ridges of tree bark.
With little more than a week remaining before Christmas in the Valley, it was time to coat the sculpture with a metal powder coat finish to replicate the texture of the tree. Favolise used a dark brown color as the base and fired the casing up in the oven before brushing the branching pattern of bark with a white powder coat.
Still, Favolise’s work wasn’t quite done. The sculpture was missing the hole left on the front of the tree from its cut limb. Without it, Favolise said it wouldn’t be authentic. So he spent three days cutting, shaping and fitting 35 pieces to craft the feature on the exterior of the sculpture.
In the final stages of the project, Favolise secured the base and top disc to the sculpture and textured the sculpture with the final metal compound before putting it in the oven to apply a final finish. Just hours before the Christmas in the Valley kickoff, Chris Wilke of K&R Graphics wrapped the memorial message over the placard.
Comments / 0